Oki has been active in cost-effective toner-based textile transfer printing for over a decade. Digital Textile Printer spoke to Rob Brown, head of European business development for Oki Europe about how that business began, how it developed and where it’s going
How long have you been selling into the textile transfer printing market? What was the motivation/goal at that time and who were the customers?
Oki Europe began introducing dedicated textile transfer printers with white toner in 2012, which crucially enabled transfers onto coloured textiles alongside white garments. Oki LED CMYK toner printers had however been used for several years prior to create effective textile transfers. Our motivation was to offer an entry-level professional digital transfer solution for short runs, both in the textiles market but in other sectors as well. Alongside t-shirt production being a significant market for us, it’s also possible to transfer to metal, wood and acrylics.
How has that part of your business grown and developed since then? Who buys/uses this kind of technology now?
White toner technology quickly enabled us to offer the world’s number one toner transfer print device, thanks to ease-of-use, mess free, fast and high quality results for customers. With particular demand for t-shirt transfers, textile decoration accounts for 90% of the applications customers use our technology for. A majority of our customer base consists of small businesses who want to offer short-run garment decoration, personalisation and/or customisation. They range from start-ups providing printing services to in-house use by schools or colleges and merchandising departments of small to medium-sized retailers. Another growing use case is custom design body art in the form of temporary tattoos, which can be transferred easily and safely to the skin.
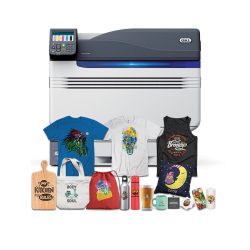
What it is and what it does – an Oki printer with samples
What was the impact of the pandemic on this business? Do you see signs of broader trends such as re-shoring and does this present an additional opportunity in the UK/Europe?
There was increase in demand for textile transfers during the pandemic as more businesses diversified into offering a wider range of services and products. Supply chain issues meant that many organisations started to consider their product supply resilience for the first time. More businesses consequently brought printing capabilities in-house to avoid any delays or shortages. It’s a trend that we’ve seen continue as the other benefits of on-demand printing have become clear for businesses in Europe. This has included the eradication of minimum order quantities from external providers, a reduction in financial and environmental wastage costs and greater flexibility from faster turnaround times.
What further plans for the textile printing sector do you have? Will we see larger/faster and/or dedicated textile printers from Oki?
The demand for personalised textiles is increasing and is leading to shorter print runs, which is ideal for Oki technology. Our dedication to the transfer market is reflected in our continuous collaboration with partners to increase the range of fabric types and other surfaces that can be printed on. Larger and faster production machines often don’t suit businesses due to the regular maintenance required between jobs. Our technology is clean, easy, fast and most importantly reliable. Customers could produce 50 t-shirts in the space of a day, leave the machine turned off for a week and then return to the device and produce the same quality without any cleaning beforehand or reliability worries.
What are the key components and advantages of the Oki offering?
White toner is undoubtedly a key advantage of Oki devices. Highly personalised designs can be transferred onto a wide range of substrates, with outstanding high density white decorations or a functional white backing layer on clear and coloured materials. White-trapping features can achieve finer, more precise graphic details on dark backgrounds. Simultaneously, our technology can use true black in place of composite black to provide crisper results. At the core of this is heat transfer media, which is the key to printing brilliant colour, opaque white and true black on garments and hard surfaces all at the same time, quickly and cost-effectively.